A injetora de plástico desempenha um papel crucial na indústria de transformação.
Este guia completo abordará todos os aspectos relevantes das injetoras, desde os diferentes tipos até a manutenção e o mercado para esses equipamentos.
Se você está considerando adquirir uma injetora usada, nova ou simplesmente quer entender melhor sobre elas, continue conosco.
A origem da injetora de plástico
A primeita injetora
A história das injetoras de plástico tem suas raízes no início do século XX, um período marcado pela ascensão da indústria de plásticos e pela busca por métodos eficientes de produção.
Estima-se que a primeira tentativa de moldagem de plástico através de injeção tenha ocorrido por volta da década de 1920.
Nessa época, James Watson Hendry é frequentemente creditado como um dos pioneiros no desenvolvimento das injetoras de plástico.
Hendry, engenheiro e inventor, patenteou um dos primeiros processos de injeção de plástico em 1936, introduzindo a ideia de usar uma rosca para extrusão e injeção de plástico em um molde.
A verdadeira revolução na indústria de plásticos ocorreu na década de 1940, com o desenvolvimento da primeira injetora totalmente automática.
Hyatt, uma empresa americana, é reconhecida por ter lançado uma das primeiras máquinas automáticas de injeção de plástico em 1946.
Essa inovação permitiu uma produção mais rápida e eficiente, dando início a uma nova era na fabricação de produtos plásticos.
A evolução das injetoras
A trajetória das injetoras de plástico é marcada por uma evolução contínua que transformou radicalmente a forma como os produtos plásticos são fabricados.
Desde os modelos iniciais até as tecnologias avançadas de hoje, cada etapa representou um salto significativo em termos de eficiência, precisão e controle sobre o processo de injeção.
Nos primeiros modelos de injetoras plásticas, inspirados nas inovações de James Watson Hendry e da Hyatt, a operação era predominantemente manual e simplificada.
As máquinas de injeção da década de 1940, como as introduzidas pela Hyatt, já representavam uma melhoria substancial com sua automação parcial, mas ainda dependiam em grande parte da intervenção humana para ajustes e controle.
As injetoras nos dias atuais
Com o avanço da tecnologia computadorizada e da automação industrial nas últimas décadas, as injetoras de plástico experimentaram transformações significativas.
As máquinas modernas, em contraste com seus antecessores, são altamente automatizadas e precisas, reduzindo a necessidade de intervenção manual e aumentando a eficiência produtiva.
Os sistemas de controle CNC (Controle Numérico Computadorizado) revolucionaram a operação das injetoras, permitindo ajustes finos e personalizados com precisão milimétrica.
Isso não apenas melhorou a qualidade dos produtos finais, mas também reduziu o desperdício de material, tornando o processo mais econômico e sustentável.
Além disso, a integração de sensores e tecnologias de monitoramento em tempo real transformou a maneira como as injetoras são operadas e mantidas.
Os operadores agora têm acesso a dados em tempo real sobre o processo de injeção, permitindo um monitoramento mais eficaz e a detecção precoce de possíveis problemas ou falhas.
Oque é uma injetora de plástico?
Uma injetora de plástico é a máquina responsável por transformar o plástico granulado (matéria-prima) em produtos como brinquedos, embalagens, peças automotivas e diversos outros itens que fazem parte do nosso cotidiano.
A injetora de plástico é uma máquina composta por diversos componentes e sistemas que trabalham em conjunto para garantir a eficiência e precisão na produção.
No entanto, o conceito básico de uma injetora é bastante simples: ela transforma o plástico granulado em peças sólidas através de um processo de aquecimento, injeção e resfriamento do material.
Veja a seguir, como funciona na prática uma injetora.
Como funciona uma injetora de plástico?
A alta pressão garante que o plástico preencha todas as cavidades dentro do molde, garantindo uma peça final de alta qualidade e precisão.
Após a injeção do plástico no molde, o material começa a esfriar e solidificar, assumindo a forma desejada.
Esse processo de resfriamento é crucial para garantir a estabilidade e resistência da peça produzida.
Por fim, a peça é retirada do molde e está pronta para ser utilizada.
Na maioria dos casos, porém, é exigido um acabamento que pode ser manual ou automatizado para retirar aparas ou rebarbas remanescentes do processo de inejção.
Esse ciclo de aquecimento, injeção e resfriamento se repete continuamente, permitindo que a injetora de plástico produza uma grande quantidade de peças em um curto espaço de tempo, tornando-a uma máquina altamente eficiente e produtiva.
Quais os tipos de injetora de plástico?
No mundo da indústria de plásticos, a escolha da injetora certa é fundamental para garantir eficiência, precisão e qualidade na produção.
As injetoras de plástico podem ser classificadas de acordo com o sistema utilizado:
Hidráulicas:
- -Utilizam sistemas hidráulicos para operar.
- São ideais para produções de médio e grande porte.
- Oferecem alta pressão e são robustas.
- Podem ser mais lentas em comparação com outros tipos.
Elétricas:
- Utilizam sistemas elétricos para operar, sendo mais eficientes energeticamente.
- Proporcionam uma operação mais silenciosa e precisa.
- São ideais para produções de precisão e peças menores.
- Geralmente possuem ciclos de injeção mais rápidos.
Híbridas:
- Combinação de sistemas hidráulicos e elétricos.
- Oferecem uma combinação de força e eficiência.
- São versáteis e adequadas para uma variedade de aplicações.
- Permitem economia de energia em comparação com as injetoras puramente hidráulicas.
Além do sistema de “força” a ser utilizado, existem também diferentes tipos de moldagem:
Duas Placas (ou Bicameral):
- Possuem duas placas móveis que se afastam após o ciclo de injeção.
- Ideal para peças maiores e moldes complexos.
- Facilitam a extração da peça moldada.
Três Placas (ou Tricameral):
- Possuem três placas móveis que se movimentam independentemente.
- Permite a extração da peça moldada e do canal de injeção separadamente.
- São adequadas para moldes com múltiplas cavidades ou peças com insertos.
Multicomponente (ou Bi-injeção):
- Capazes de injetar dois materiais diferentes em uma única operação.
- Permitem a criação de peças com diferentes cores ou materiais em uma única etapa.
- São versáteis e adequadas para aplicações que requerem combinação de materiais.
Cada tipo de máquina possui suas próprias características e benefícios, tornando-se essencial entender as diferenças entre elas para fazer a escolha mais adequada para cada aplicação.

Principais partes e componentes de uma injetora de plástico
A produção de peças plásticas por meio do processo de injeção é um sistema complexo que envolve uma série de equipamentos e componentes interconectados.
Cada etapa desse processo, desde o design do molde até a operação das injetoras e o controle dos parâmetros de produção, desempenha um papel crucial na qualidade e eficiência da produção.
Neste segmento, vamos explorar alguns dos equipamentos e partes fundamentais desse processo, dando ênfase à importância de cada um e como eles contribuem para o sucesso da operação.
1. Molde para injetoras
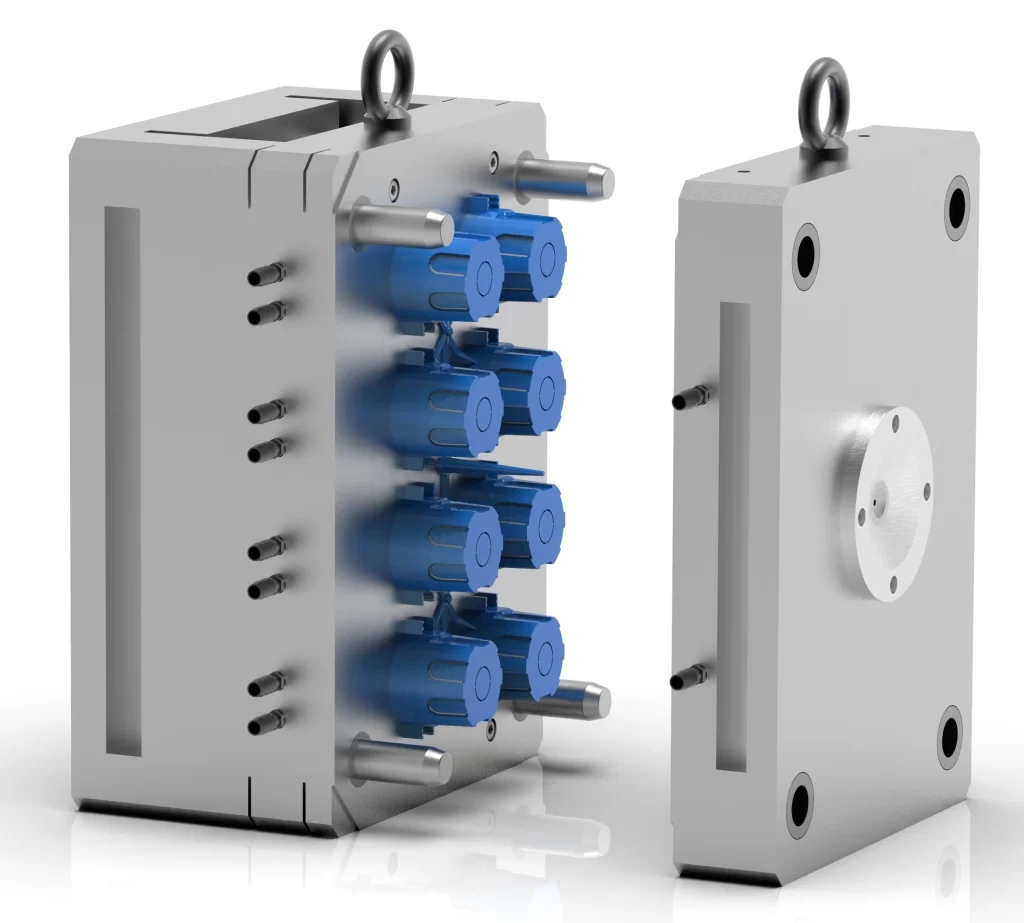
Os moldes são peças centrais no processo de injeção de plásticos, atuando como a “forma” que determina a aparência e as características das peças produzidas.
Imagine um molde como um molde de bolo, mas em vez de bolo, ele é preenchido com plástico derretido que se solidifica para formar uma peça plástica.
Essa “forma” é projetada meticulosamente para produzir peças com precisão, detalhes e acabamento desejados.
Tipos de Moldes
Existem diversos tipos de moldes, cada um adequado para diferentes aplicações e volumes de produção.
Os moldes podem ser classificados em moldes de cavidade única, moldes de cavidades múltiplas e moldes de cavidades familiares.
Os moldes de cavidade única produzem uma peça por vez, enquanto os moldes de cavidades múltiplas produzem várias peças simultaneamente.
Já os moldes de cavidades familiares produzem peças diferentes em uma única operação, otimizando o tempo e reduzindo custos.
Materiais dos Moldes
Os moldes são geralmente fabricados em aço ou alumínio, materiais que oferecem durabilidade e resistência necessárias para suportar as pressões e temperaturas do processo de injeção.
O tipo de material escolhido depende das especificações do produto, do volume de produção e da durabilidade desejada.
Moldes de aço são ideais para produções de alto volume e peças com detalhes complexos, enquanto moldes de alumínio são mais adequados para prototipagem e produções de menor volume.
Projeto e Fabricação dos Moldes
O projeto e fabricação dos moldes são etapas críticas que requerem expertise e precisão.
Um molde bem projetado leva em consideração todos os aspectos da peça final, incluindo dimensões, tolerâncias, acabamento superficial e pontos de injeção.
O processo de fabricação envolve usinagem de alta precisão, tratamentos térmicos e acabamento para garantir que o molde atenda às especificações e funcione de forma eficiente durante a produção.
Manutenção e Cuidados com os Moldes
A manutenção adequada dos moldes é essencial para garantir sua durabilidade e desempenho ao longo do tempo. Isso inclui limpeza regular, inspeção de desgaste, reparos e ajustes necessários.
A manutenção preventiva é fundamental para prevenir falhas inesperadas e assegurar que o molde esteja sempre em condições ótimas de funcionamento.
Além disso, a escolha de um fornecedor confiável e experiente na fabricação e manutenção de moldes é crucial para garantir a qualidade e eficiência da produção.
Para mais informações, criamos um post exclusivo sobre moldes, você pode acessá-lo clicando aqui.
2. Resfriamento / Refrigeração
O controle eficiente da temperatura é um dos aspectos mais críticos no processo de injeção de plásticos.
O plástico derretido precisa ser resfriado adequadamente para solidificar e formar a peça desejada.
Para isso, sistemas de resfriamento ou refrigeração são utilizados para manter a temperatura do plástico e do molde dentro dos parâmetros ideais.
Vamos explorar mais sobre a importância desses sistemas e como eles influenciam a qualidade e eficiência da produção.
Importância do Resfriamento / Refrigeração
O resfriamento das peças e o correto dimensionamento da refrigeração adequados são essenciais para garantir a qualidade das peças produzidas.
Se o plástico não for resfriado corretamente, podem ocorrer deformações, tensões internas e outros defeitos que afetam a qualidade e durabilidade da peça.
Além disso, o controle preciso da temperatura durante o processo de injeção ajuda a otimizar o ciclo de produção, reduzindo o tempo necessário para solidificar o plástico e, consequentemente, aumentando a produtividade.
Tipos de Sistemas de Resfriamento / Refrigeração
Existem diferentes tipos de sistemas de resfriamento/refrigeração que podem ser utilizados no processo de injeção de plásticos, sendo os mais comuns os sistemas de água gelada e os sistemas termorreguladores.
Sistemas de Água Gelada:
Utilizam água resfriada para manter a temperatura do molde e do plástico dentro dos parâmetros ideais. São sistemas eficientes e amplamente utilizados em indústrias de grande porte.
Sistemas Termorreguladores:
São unidades compactas que controlam a temperatura do molde e do plástico por meio de fluidos térmicos. São ideais para aplicações que requerem maior precisão e controle da temperatura.
Manutenção dos Sistemas de Resfriamento / Refrigeração
Assim como outros componentes do processo de injeção de plásticos, os sistemas de resfriamento/refrigeração requerem manutenção adequada para garantir seu funcionamento eficiente e confiável.
Isso inclui a limpeza regular dos equipamentos, verificação de vazamentos, substituição de peças desgastadas e calibração dos sensores e controles.
A manutenção preventiva é crucial para prevenir falhas, reduzir o tempo de inatividade e prolongar a vida útil dos equipamentos.
Integração com o Processo de Injeção
Os sistemas de resfriamento/refrigeração estão intimamente integrados ao processo de injeção de plásticos, trabalhando em conjunto com outros componentes como os moldes, as injetoras e os sistemas de controle.
Uma integração eficiente permite um controle preciso da temperatura durante todo o processo, garantindo a qualidade e eficiência da produção.
Além disso, a implementação de tecnologias avançadas de controle e monitoramento pode ajudar a otimizar o desempenho dos sistemas de resfriamento/refrigeração e do processo como um todo.
3. Elétrica
A parte elétrica das injetoras de plástico é responsável por fornecer a energia necessária para o funcionamento dos motores, controles e sistemas auxiliares.
O sistema elétrico é vital para o controle preciso dos movimentos dos componentes da máquina, como o parafuso e o cilindro, garantindo a eficiência e a qualidade do processo de injeção.
Vamos explorar mais sobre a importância da parte elétrica e como ela influencia no desempenho das injetoras.
Principais componentes elétricos de uma injetora
As injetoras de plástico possuem uma variedade de componentes elétricos que desempenham funções específicas no processo de injeção.
Alguns dos componentes mais importantes incluem:
- Motores: Responsáveis por acionar os movimentos dos componentes da máquina, como o parafuso e o cilindro.
- Controladores: Dispositivos que monitoram e controlam os parâmetros do processo, como temperatura, pressão e velocidade.
- Sensores: Equipamentos que captam informações sobre o processo e fornecem dados para os controladores.
- Painéis de Controle: Interfaces que permitem aos operadores configurar e monitorar o funcionamento da máquina.
Manutenção Elétrica
A manutenção elétrica é crucial para garantir o funcionamento seguro e confiável das injetoras de plástico.
Isso inclui a inspeção regular dos componentes elétricos, verificação de conexões, limpeza de contatos e substituição de peças desgastadas.
Além disso, a calibração e o ajuste dos controladores e sensores são fundamentais para manter a precisão e a eficiência do processo de injeção.
Manutenção Elétrica
A manutenção elétrica é crucial para garantir o funcionamento seguro e confiável das injetoras de plástico.
Isso inclui a inspeção regular dos componentes elétricos, verificação de conexões, limpeza de contatos e substituição de peças desgastadas.
Além disso, a calibração e o ajuste dos controladores e sensores são fundamentais para manter a precisão e a eficiência do processo de injeção.
Segurança Elétrica
A segurança elétrica é uma preocupação importante na operação das injetoras de plástico.
É essencial seguir as normas e regulamentações de segurança elétrica, incluindo a instalação adequada de dispositivos de proteção, como disjuntores e fusíveis, e a realização de inspeções e testes periódicos para garantir que todos os equipamentos estejam em conformidade e operem de forma segura.
4. Eletrônica
A parte eletrônica das injetoras de plástico refere-se aos sistemas de controle computadorizado, sensores e dispositivos eletrônicos avançados que auxiliam no monitoramento e controle do processo de injeção.
A eletrônica moderna desempenha um papel crucial na automação, otimização e eficiência das operações de injeção.
Vamos explorar mais sobre a importância da parte eletrônica e como ela contribui para o sucesso das operações.
Sistemas Eletrônicos Avançados
Os sistemas eletrônicos avançados das injetoras de plástico incluem:
- Controladores CNC (Controle Numérico Computadorizado): Permitem o controle preciso dos movimentos e parâmetros do processo.
- Sistemas de Monitoramento em Tempo Real: Utilizam sensores e câmeras para monitorar o processo e detectar problemas ou anomalias.
- Integração de Sistemas: A integração entre os sistemas eletrônicos, elétricos e mecânicos permite uma operação mais eficiente e automatizada da máquina.
Benefícios da Eletrônica Moderna
A eletrônica moderna traz uma série de benefícios para as operações de injeção de plástico, incluindo:
- Automatização: Automatização de tarefas repetitivas, aumentando a produtividade e reduzindo erros.
- Otimização: Otimização dos parâmetros do processo para melhorar a qualidade das peças e reduzir o desperdício.
- Monitoramento: Monitoramento em tempo real do processo para detecção precoce de problemas e manutenção proativa.
- Flexibilidade: Maior flexibilidade na produção, permitindo mudanças rápidas de configuração e adaptação a diferentes tipos de peças e materiais.
- Integração Eletrônica e Elétrica
A integração eficiente entre os sistemas eletrônicos e elétricos é fundamental para o desempenho e a eficiência das injetoras de plástico.
A comunicação e a sincronização entre os controladores, sensores, motores e outros componentes garantem um controle preciso e confiável do processo de injeção, contribuindo para a qualidade das peças produzidas e a eficiência operacional.
5. Rosca sem fim
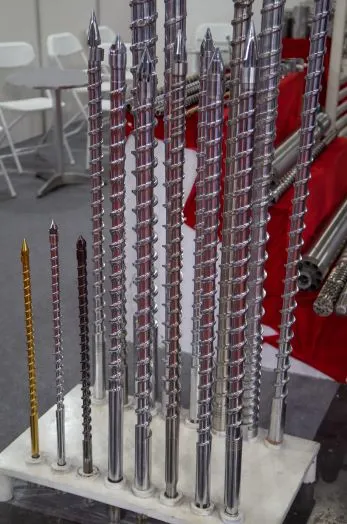
A rosca sem fim, também conhecida como parafuso de injeção, é um componente essencial da unidade de plastificação de uma máquina injetora.
Sua função principal é plastificar e homogeneizar o material plástico antes de sua injeção no molde.
A rosca sem fim é composta por três zonas distintas:
Zona de Alimentação: O material sólido (granulado) é alimentado e transportado para frente.
Zona de Compressão: Aqui, ocorre a compactação e começa a derreter devido ao calor gerado pelo atrito e pelos aquecedores externos.
Zona de Dosagem: Aqui, o plástico já fundido fundido é homogeneizado e preparado para ser injetado no molde.
A importância da rosca sem fim no processo de injeção
A rosca sem fim desempenha várias funções cruciais que impactam diretamente a qualidade e a eficiência do processo de injeção plástica:
- Plastificação do Material: A rosca sem fim transforma os grânulos de plástico em uma massa fundida uniforme, garantindo uma boa plastificação do material.
- Homogeneização: Durante o movimento de rotação, a rosca sem fim mistura o material fundido de maneira uniforme, eliminando pontos de fraqueza e garantindo a consistência do produto final.
- Pressurização: A rosca gera a pressão necessária para injetar o material fundido no molde, assegurando que o molde seja preenchido corretamente e sem defeitos.
Tipos de roscas sem fim
Existem vários tipos de roscas sem fim, cada uma projetada para atender a diferentes necessidades e tipos de materiais plásticos:
- Rosca Convencional: É o tipo mais comum e utilizado em aplicações gerais. Possui uma geometria básica que se adapta a diversos materiais.
- Rosca de Alta Performance: Projetada para materiais específicos, como plásticos técnicos de alta viscosidade. Proporciona melhor plastificação e homogeneização.
- Rosca Bari-métrica: Utilizada para materiais com alta sensibilidade ao cisalhamento, como plásticos reforçados com fibras. Minimiza a degradação do material.
- Rosca de Mistura: Possui elementos de mistura incorporados para melhorar a homogeneidade do material fundido, especialmente útil para compósitos e blendas.
Benefícios da utilização de uma rosca sem fim de qualidade
A escolha de uma rosca sem fim adequada pode trazer vários benefícios para o processo de injeção plástica:
- Melhoria na Qualidade do Produto: Uma rosca bem projetada assegura uma plastificação uniforme e uma mistura homogênea, resultando em produtos finais de alta qualidade.
- Redução de Ciclos de Produção: Com uma plastificação eficiente, o tempo de ciclo de produção é reduzido, aumentando a produtividade.
- Economia de Energia: Uma rosca otimizada requer menos energia para plastificar o material, resultando em economia de custos operacionais.
- Maior Durabilidade: Roscas de alta qualidade possuem uma maior resistência ao desgaste e à corrosão, prolongando a vida útil do componente e reduzindo a necessidade de manutenção.
Cuidados e manutenção da rosca sem fim
Para garantir o desempenho ótimo da rosca sem fim, é fundamental realizar uma manutenção adequada e seguir algumas práticas recomendadas:
- Limpeza Regular: Manter a rosca limpa e livre de resíduos de material plástico evita o acúmulo de contaminantes que podem comprometer a qualidade da plastificação.
- Inspeções Periódicas: Realizar inspeções regulares para identificar sinais de desgaste ou danos, permitindo intervenções preventivas antes que problemas maiores ocorram.
- Lubrificação Adequada: Utilizar lubrificantes apropriados para reduzir o atrito e o desgaste entre a rosca e o cilindro.
- Armazenamento Correto: Quando não estiver em uso, a rosca deve ser armazenada em condições adequadas para evitar corrosão e outros danos.
Componentes acessórios para injeção de plástico
1. Secagem
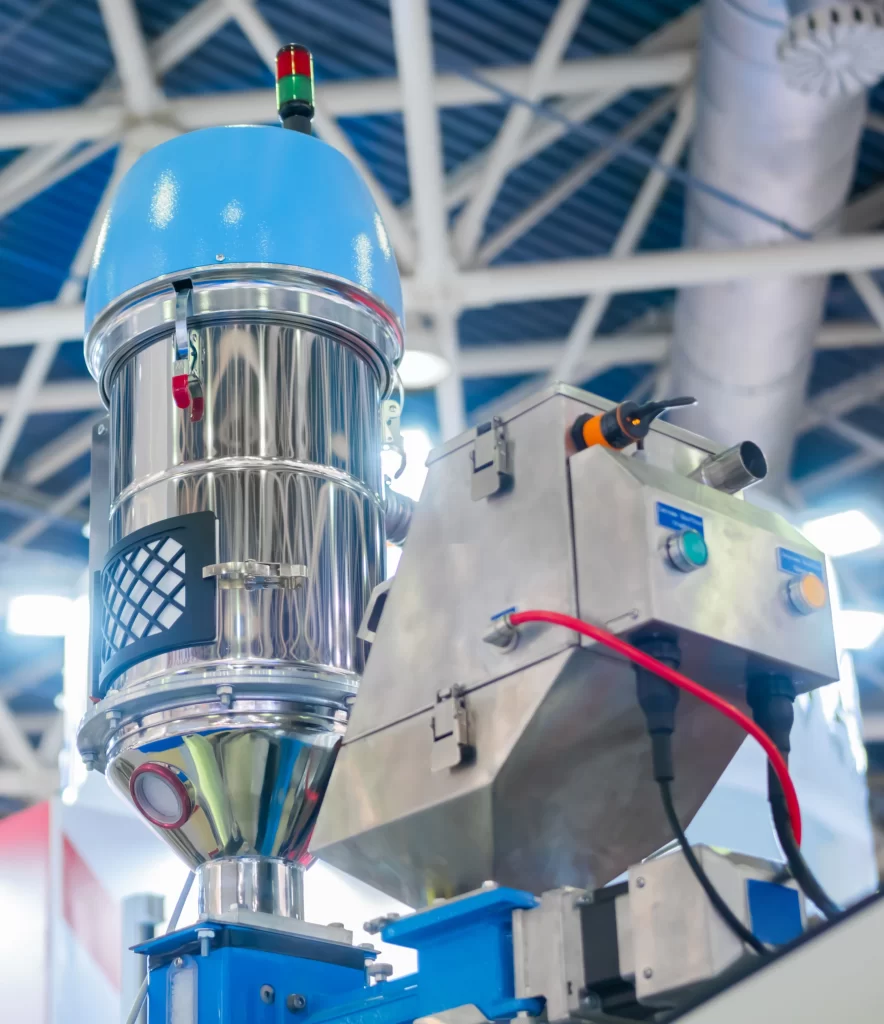
A secagem é uma etapa fundamental no processo de injeção de plásticos, especialmente quando se utiliza materiais termoplásticos.
Antes de serem injetados, os grânulos ou pellets de plástico devem ser secos para remover a umidade que pode afetar a qualidade e as propriedades finais das peças produzidas.
Vamos explorar mais sobre a importância da secagem, os métodos utilizados e como isso influencia na qualidade da produção.
Importância da Secagem
A umidade presente nos grânulos de plástico pode causar uma série de problemas durante o processo de injeção, como porosidade, defeitos superficiais, redução da resistência mecânica e alterações nas propriedades físicas do material.
A secagem adequada é essencial para garantir a qualidade e a consistência das peças produzidas, bem como para evitar problemas de processo e desperdício de material.
Métodos de Secagem
Existem diferentes métodos de secagem que podem ser utilizados para remover a umidade dos grânulos de plástico:
Secagem por Ar Quente: Utiliza ar quente para evaporar a umidade dos grânulos. É um método rápido e eficiente, geralmente realizado em secadores de ar quente.
Secagem a Vácuo: Utiliza um vácuo para reduzir a pressão atmosférica e acelerar a evaporação da umidade. É um método mais lento, mas que pode ser mais eficaz para materiais sensíveis.
Secagem por Desumidificação: Utiliza um processo de desumidificação para remover a umidade do ar e dos grânulos. É um método eficiente para ambientes com alta umidade relativa.
Equipamentos de Secagem
Os equipamentos de secagem são projetados especificamente para realizar o processo de secagem dos grânulos de plástico de forma eficiente e confiável.
Alguns dos equipamentos mais comuns incluem:
Secadores de Ar Quente: Equipamentos que utilizam ar quente para secar os grânulos de plástico. Podem ser de leito fluidizado, estufa ou tambor rotativo.
Secadores a Vácuo: Equipamentos que utilizam um vácuo para acelerar a evaporação da umidade dos grânulos de plástico.
Secadores por Desumidificação: Equipamentos que utilizam um processo de desumidificação para remover a umidade do ar e dos grânulos.
Controle e Monitoramento da Secagem
O controle e o monitoramento adequados do processo de secagem são fundamentais para garantir a eficácia da secagem e a qualidade dos grânulos de plástico.
Isso inclui o monitoramento da temperatura e do tempo de secagem, a verificação da umidade residual nos grânulos e a calibração adequada dos equipamentos de secagem.
A manutenção regular dos equipamentos e a substituição de peças desgastadas são essenciais para garantir o funcionamento confiável e seguro dos equipamentos de secagem.
Se quiser saber mais sobre secagem, veja este outro post.
Dosadores e Misturadores de Materiais
Os dosadores e misturadores de materiais desempenham um papel crucial no processo de injeção de plásticos, garantindo a dosagem correta e a homogeneidade da mistura de materiais, aditivos e pigmentos.
Esses equipamentos são fundamentais para a preparação adequada da matéria-prima antes do processo de injeção.
Funcionamento e importância
Os dosadores e misturadores operam em conjunto para preparar a mistura de materiais antes de serem introduzidos no processo de injeção.
Os dosadores medem e dosam os grânulos de plástico, aditivos e pigmentos na quantidade precisa, enquanto os misturadores asseguram a homogeneidade da mistura.
Essa preparação adequada é essencial para garantir a qualidade e as propriedades desejadas das peças produzidas, além de contribuir para a eficiência e consistência do processo.
Tipos de Dosadores e Misturadores
Existem diversos tipos de dosadores e misturadores disponíveis no mercado, cada um com suas características e aplicações específicas:
Dosadores Gravimétricos: Utilizam a medição do peso para dosar os materiais, proporcionando uma dosagem precisa e confiável.
Dosadores Volumétricos: Utilizam a medição do volume para dosar os materiais, sendo adequados para materiais de fluxo constante.
Misturadores de Tambor: Utilizam tambores rotativos para misturar os materiais de forma homogênea, sendo ideais para grandes volumes.
Misturadores Estáticos: Utilizam elementos estáticos para promover a mistura dos materiais, sendo mais compactos e eficientes para volumes menores.
Moinhos e Granuladores
Os moinhos e granuladores são equipamentos utilizados para triturar e transformar os resíduos e peças defeituosas de plástico em pequenos grânulos ou pellets.
Esses equipamentos desempenham um papel importante na redução de desperdícios e custos, permitindo a reutilização dos materiais reciclados no processo de injeção.
Processo de Moagem e Granulação
O processo de moagem e granulação envolve a trituração dos resíduos de plástico em pequenas partículas e a transformação dessas partículas em grânulos ou pellets.
Os moinhos utilizam lâminas afiadas para triturar os materiais, enquanto os granuladores utilizam rotores para transformar os materiais triturados em grânulos.
Esse processo é fundamental para a reciclagem e reutilização dos materiais, contribuindo para a sustentabilidade e redução dos impactos ambientais.
Sistemas de Alimentação Automática
Os sistemas de alimentação automática são projetados para alimentar automaticamente os grânulos de plástico e outros materiais nos equipamentos de secagem, dosagem e injeção.
Esses sistemas contribuem para a redução da intervenção manual, melhorando a eficiência do processo e garantindo uma alimentação constante e precisa dos materiais.
Vantagens da Alimentação Automática
A alimentação automática dos materiais proporciona uma série de vantagens significativas:
Redução de Erros Humanos: Minimiza os erros e inconsistências associados à alimentação manual dos materiais.
Otimização dos Tempos de Ciclo: Melhora a eficiência e produtividade do processo, reduzindo os tempos de ciclo.
Minimização dos Desperdícios: Garante uma alimentação precisa dos materiais, reduzindo os desperdícios e custos associados.
Melhoria da Qualidade das Peças: Contribui para a produção de peças de plástico de alta qualidade e consistência.
2. Sistemas de Filtragem e Purificação
Os sistemas de filtragem e purificação são essenciais para remover impurezas, contaminantes e partículas indesejadas do plástico derretido antes da injeção.
Esses sistemas garantem a qualidade e a pureza do material utilizado, contribuindo para a produção de peças de plástico de alta qualidade e durabilidade.
Funcionamento e Benefícios
Os sistemas de filtragem e purificação utilizam diferentes métodos e tecnologias para remover as impurezas do plástico derretido:
Filtros de Malha: Utilizam uma malha fina para filtrar as partículas indesejadas do plástico derretido.
Filtros de Cartucho: Utilizam cartuchos filtrantes para remover impurezas e contaminantes do plástico derretido.
Sistemas de Purificação a Vácuo: Utilizam um vácuo para remover gases e vapores indesejados do plástico derretido.
A utilização desses sistemas proporciona uma série de benefícios, incluindo a melhoria da qualidade das peças produzidas, a redução de defeitos e a prolongação da vida útil dos equipamentos.
Sistemas de Ventilação e Exaustão
Os sistemas de ventilação e exaustão são projetados para controlar a ventilação e a exaustão dos gases e vapores gerados durante o processo de injeção.
Esses sistemas garantem um ambiente de trabalho seguro e saudável, removendo os gases e vapores tóxicos e garantindo uma boa circulação do ar no local de trabalho.
Importância da Ventilação e Exaustão
A ventilação e exaustão adequadas são fundamentais para proteger a saúde dos trabalhadores e prevenir a exposição a substâncias nocivas.
Além disso, esses sistemas contribuem para a manutenção da qualidade do ar no ambiente de trabalho, evitando a acumulação de gases e vapores e reduzindo o risco de explosões e incêndios.
A boa circulação do ar também ajuda a controlar a temperatura e a umidade do ambiente, proporcionando condições de trabalho mais confortáveis e produtivas.
Manutenção das máquinas injetoras
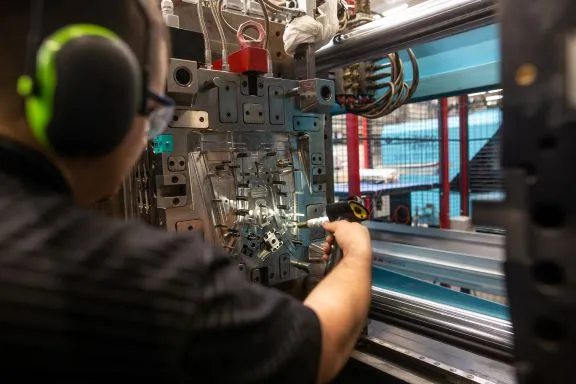
A manutenção é um aspecto crucial no processo de injeção de plásticos que abrange uma série de atividades e práticas para garantir o bom funcionamento e prolongar a vida útil dos equipamentos e componentes envolvidos.
Ela é essencial para prevenir falhas, otimizar a eficiência da produção e assegurar a segurança no ambiente de trabalho.
Vamos explorar mais detalhadamente a importância da manutenção e algumas das práticas comuns adotadas na indústria.
Tipos de Manutenção
Existem diferentes tipos de manutenção que podem ser aplicados no processo de injeção de plásticos, sendo os mais comuns a manutenção corretiva, preventiva e preditiva.
Manutenção Corretiva: Realizada após a identificação de um problema ou falha no equipamento. Embora seja eficaz para resolver problemas imediatos, pode resultar em tempo de inatividade não planejado e custos adicionais.
Manutenção Preventiva: Programada e realizada regularmente para prevenir falhas e garantir o funcionamento contínuo dos equipamentos. Inclui inspeções, limpezas e substituição de peças desgastadas.
Manutenção Preditiva: Utiliza técnicas e ferramentas para monitorar o desempenho dos equipamentos e prever possíveis falhas antes que ocorram. Isso permite intervenções proativas e reduz o tempo de inatividade.
Importância da Manutenção
A manutenção adequada é fundamental para garantir a operação segura e eficiente das injetoras de plástico.
Ela ajuda a prevenir falhas inesperadas, reduzir o tempo de inatividade, otimizar a produtividade e prolongar a vida útil dos equipamentos.
Além disso, a manutenção regular contribui para a segurança no ambiente de trabalho, assegurando que os equipamentos operem de forma segura e confiável.
Práticas de Manutenção
As práticas de manutenção podem variar dependendo dos equipamentos e das necessidades específicas de cada empresa. No entanto, algumas práticas comuns incluem:
– Realizar inspeções regulares para identificar desgastes ou danos nos equipamentos.
– Lubrificação adequada de componentes móveis para reduzir o desgaste e o atrito.
– Substituição de peças desgastadas ou danificadas antes que causem falhas no equipamento.
– Calibração de sensores e sistemas de controle para garantir precisão e confiabilidade.
– Treinamento e capacitação da equipe de manutenção para garantir que estejam atualizados com as melhores práticas e tecnologias.
Gestão de Manutenção
A gestão eficaz da manutenção envolve o planejamento, organização e controle de todas as atividades relacionadas à manutenção.
Isso inclui a definição de prioridades, alocação de recursos, acompanhamento do desempenho dos equipamentos e análise de dados para tomar decisões informadas.
A implementação de um sistema de gestão de manutenção ajuda a otimizar os processos, reduzir custos e melhorar a eficiência operacional.
Para se aprofundar mais sobre o assunto, temos um post completo e só sobre manutenção. Clique aqui e saiba mais.
O mercado atendido pela injetora
Produtos que uma injetora pode fabricar
O mercado de injeção de plástico é fascinante e abrangente, contribuindo para a criação de uma vasta gama de produtos que utilizamos em nosso dia a dia.
Vamos explorar mais sobre os produtos fabricados através deste processo e sua importância em nossa sociedade.
Diversidade de Produtos
A injeção de plástico é uma técnica versátil que nos permite transformar plástico em uma variedade incrível de produtos.
Imagine os diversos objetos que você utiliza diariamente: desde os componentes do seu carro e os eletrodomésticos em sua casa até os brinquedos das crianças e as embalagens dos alimentos que consumimos.
Muitos desses produtos são fabricados através da injeção de plástico!
Aplicações Industriais e Consumo
Os produtos fabricados por injeção de plástico são encontrados em quase todos os setores industriais e em nossas casas.
Veja alguns exemplos:
Automotivo: Os componentes automotivos incluem desde os painéis e para-choques até os pequenos suportes e engrenagens que mantêm o veículo funcionando corretamente.
Eletrodomésticos: Seja a máquina de lavar roupa, o micro-ondas, o liquidificador ou o aspirador de pó, muitos dos eletrodomésticos que facilitam nossa vida cotidiana contêm peças fabricadas por injeção de plástico.
Eletrônicos: Os dispositivos eletrônicos que utilizamos, como smartphones, tablets e computadores, contêm carcaças, conectores e outros componentes fabricados por este processo.
Embalagens: As embalagens que protegem e conservam nossos alimentos, bebidas e produtos diversos são frequentemente fabricadas por injeção de plástico. Isso inclui garrafas, potes, tampas e muito mais.
Brinquedos e Artigos de Consumo: Os brinquedos das crianças, utensílios domésticos e artigos de decoração são outros exemplos de produtos que podem ser fabricados por injeção de plástico.
Tendências e Inovações em Produtos
O mercado de injeção de plástico está sempre evoluindo e se adaptando às novas demandas da sociedade. Algumas tendências e inovações recentes incluem:
Produtos Sustentáveis: Estamos vendo um aumento na demanda por produtos ecologicamente corretos. Isso inclui o uso de plásticos reciclados ou biodegradáveis na fabricação de novos produtos, contribuindo para a sustentabilidade e redução dos impactos ambientais.
Produtos Personalizados: A personalização está em alta! A capacidade de produzir peças sob medida e customizadas de acordo com as necessidades e preferências dos clientes é uma das grandes vantagens da injeção de plástico.
Produtos Inteligentes: A tecnologia está cada vez mais presente em nossos produtos. A incorporação de tecnologia e conectividade em produtos, como dispositivos eletrônicos e componentes para Internet das Coisas (IoT), é uma tendência crescente no mercado.
Designs Inovadores: O design é uma parte essencial na criação de novos produtos.
O uso de design avançado e ergonômico permite criar produtos mais atraentes, funcionais e eficientes, melhorando a experiência do usuário.
Inovação no mercado de injetoras
O mercado de injetoras de plástico está em constante evolução, com novas tecnologias e inovações que estão transformando a maneira como as injetoras operam e como os produtos são fabricados.
Vamos explorar algumas das inovações mais surpreendentes que estão revolucionando o setor.
1. Impressão 3D em Injetoras de Plástico
A integração da impressão 3D nas injetoras de plástico está mudando o jogo!
Essa tecnologia permite a criação de protótipos rápidos, a produção de peças complexas e a personalização de produtos de forma mais eficiente e econômica.
Imagine criar um protótipo de uma peça em poucas horas e testar diferentes designs antes de iniciar a produção em larga escala.
2. Inteligência Artificial (IA) e Machine Learning
A Inteligência Artificial (IA) e o Machine Learning estão elevando o nível das injetoras de plástico!
Essas tecnologias permitem que as máquinas aprendam e se adaptem aos processos de produção, otimizando os parâmetros de injeção, reduzindo os tempos de ciclo e detectando falhas em tempo real.
Imagine uma injetora que analisa dados, aprende com os erros e faz ajustes automáticos para garantir a melhor qualidade das peças produzidas.
3. Sensores IoT e Monitoramento em Tempo Real
A era da Internet das Coisas (IoT) chegou às injetoras de plástico!
A incorporação de sensores IoT permite o monitoramento em tempo real das equipamentos e processos de produção das injetoras. Isso possibilita uma manutenção preditiva, identificando potenciais problemas antes que causem paradas não planejadas, e otimiza a eficiência operacional, ajustando os parâmetros de produção conforme necessário.
4. Energia Renovável e Sustentabilidade
A preocupação com a sustentabilidade está impulsionando a adoção de fontes de energia renovável nas injetoras de plástico.
A utilização de energia solar, eólica e outras fontes renováveis está se tornando uma realidade, contribuindo para a redução do impacto ambiental da produção e para a criação de um processo mais sustentável.
5. Realidade Virtual (RV) e Realidade Aumentada (RA)
A Realidade Virtual (RV) e a Realidade Aumentada (RA) estão sendo utilizadas para simular e otimizar os processos de injeção de plástico.
Essas tecnologias permitem treinamentos mais eficientes, design de moldes mais preciso e visualização em tempo real das operações de produção das injetoras, proporcionando uma experiência imersiva e colaborativa.
Como escolher uma injetora
A escolha de um bom equipamento que supra suas necessidades de produção e caiba no seu bolso é fundamental, seja para uma ampliação de produção e pricipalmente se você está iniciando.
Em nosso marketplace, você tem disponíveis anúncios de máquinas novas e usadas de diversos tamanhos e para diversas aplicações.

Capacidade
Ao escolher uma injetora de plástico, um dos primeiros aspectos a serem considerados é a capacidade da máquina.
Esta capacidade está diretamente relacionada ao tamanho das peças que você pretende produzir.
É essencial dimensionar a máquina de forma adequada para garantir que ela seja capaz de lidar com as demandas do seu projeto.
Ao avaliar a capacidade da injetora, leve em conta não apenas o peso ou volume das peças, mas também outros fatores como a complexidade do molde e o ciclo de produção desejado.
Uma máquina com capacidade insuficiente pode resultar em ciclos de produção mais longos e menor eficiência, enquanto uma máquina superdimensionada pode representar um investimento desnecessário.
Analise cuidadosamente as especificações técnicas e as necessidades do seu projeto para escolher uma injetora com a capacidade ideal.
Isso garantirá que você obtenha o melhor desempenho e produtividade, otimizando os resultados e o retorno sobre o investimento na máquina.
Olhar para o Futuro
Ao investir em uma injetora de plástico, é comum focar nas necessidades imediatas e no presente, mas é crucial também pensar no futuro.
Uma das armadilhas mais comuns na escolha da máquina é não considerar as possíveis expansões ou mudanças no portfólio de produtos da empresa.
A capacidade da máquina deve não apenas atender às demandas atuais, mas também estar alinhada com as expectativas de crescimento e diversificação do negócio.
Pode ser que, no futuro, você queira produzir peças maiores ou até mesmo desenvolver novos produtos que exijam uma capacidade maior da injetora.
Por isso, ao escolher a capacidade da máquina, é importante pensar estrategicamente e avaliar as possibilidades de expansão.
Considere não apenas o que você precisa agora, mas também o que pode vir a precisar nos próximos anos.
Essa visão de futuro permitirá que você faça um investimento mais sustentável e evite a necessidade de substituir ou atualizar a máquina em um curto período de tempo.
Planejar com antecedência é a chave para garantir que sua injetora atenda às demandas futuras e ofereça um bom retorno sobre o investimento a longo prazo.
Espaço
Ao adquirir uma injetora de plástico, um dos aspectos muitas vezes negligenciados, mas de extrema importância, é o espaço físico necessário para instalação e operação da máquina.
As injetoras de plástico variam em tamanho, mas em média, uma máquina de porte médio pode ter dimensões aproximadas de 3,5m x 1,5m x 2m (Largura x Profundidade x Altura).
No entanto, é essencial lembrar que o espaço necessário vai além das dimensões da própria máquina.
Você também deve considerar o espaço para armazenamento de matéria-prima, equipamentos auxiliares, ferramentas e acessórios.
Além disso, é importante ter um espaço adequado para acondicionar as peças prontas, bem como para a circulação segura dos operadores e manutenção da máquina.
Antes de realizar a compra, meça e avalie cuidadosamente o espaço disponível em sua instalação, considerando não apenas as dimensões da injetora, mas também todos os espaços adicionais necessários para uma operação eficiente e segura.
Planejar adequadamente o layout e a disposição dos equipamentos e materiais garantirá um ambiente de trabalho organizado, otimizado e que atenda às necessidades operacionais da sua injetora de plástico.
Reputação do Fabricante
A reputação do fabricante é um fator crucial na escolha de uma injetora de plástico.
Optar por uma máquina de uma marca reconhecida no mercado pode oferecer diversas vantagens, como garantia de qualidade, confiabilidade e suporte técnico especializado.
Marcas renomadas geralmente investem em pesquisa e desenvolvimento, oferecendo máquinas com tecnologias avançadas e atualizações constantes para atender às demandas do mercado.
Por outro lado, ao considerar uma máquina de uma marca desconhecida, é importante ser cauteloso e realizar uma pesquisa detalhada.
Embora possam oferecer preços mais atrativos, as máquinas de marcas menos conhecidas podem apresentar maior risco em termos de qualidade, durabilidade e disponibilidade de peças de reposição.
Além disso, pode haver dificuldades em obter suporte técnico e assistência especializada, o que pode comprometer a operação e manutenção da máquina a longo prazo.
Ao escolher sua injetora de plástico, é recomendado priorizar marcas com boa reputação no mercado.
Consulte as avaliações de clientes, pesquise sobre a história e o tempo de atuação do fabricante, e busque referências de outras empresas que utilizam máquinas da mesma marca.
Essa análise cuidadosa proporcionará maior segurança e tranquilidade na sua decisão de investimento.
Marcas fabricantes de injetora mais conhecidas
Arburg: Fundada na Alemanha, a Arburg é uma das líderes globais no mercado de máquinas de injeção de plástico, conhecida por sua tecnologia avançada e soluções personalizadas.
Engel: Originária da Áustria, a Engel é outra marca icônica que se destaca pela inovação e pela ampla variedade de máquinas de injeção de plástico de alta qualidade.
Husky Injection Molding Systems: Com sede no Canadá, a Husky é reconhecida pela sua expertise em sistemas de injeção para a indústria de embalagens.
Sumitomo (SHI) Demag: Com origem no Japão e Alemanha, a Sumitomo Demag é conhecida pela sua tecnologia avançada e pela ampla gama de máquinas de injeção de plástico.
Romi: Uma das empresas mais tradicionais e reconhecidas do mercado brasileiro, a Romi oferece uma ampla gama de máquinas de injeção de plástico com tecnologia avançada.
Haitian: Com presença global, a Haitian é uma das maiores fabricantes de máquinas de injeção de plástico do mundo e possui uma forte atuação no mercado brasileiro, oferecendo máquinas de alta performance a preços competitivos.
Plastimax: Especializada na fabricação de máquinas injetoras de pequeno e médio porte, a Plastimax é uma empresa brasileira que se destaca pela qualidade, confiabilidade e pelo suporte ao cliente.
Custos
Agora vamos falar sobre algo muito importante: os custos a serem avaliados na compra e operação de uma injetora de plástico.
Essa etapa é fundamental para garantir um investimento consciente e rentável, evitando surpresas financeiras e garantindo uma operação sustentável a longo prazo.
Tanto no processo de compra / instalção do equipamento, quanto na própria operação, sempre existirão os custos “invisíveis”.
Mesmo aos olhos atentos dos profissionais mais experientes, sempre conte com alguns custos emergenciais e não planejados.
Vamos agora, dar um panorama geral sobre os custos mais comuns na compra, instalação e operação de uma máquina injetora.
Valor da injetora
Vamos iniciar pelo básico. O valor de uma injetora de plástico. Geralmente este é o primeiro item a ser analisado.
Ao avaliar o preço de uma injetora de plástico, é fundamental adotar uma abordagem abrangente e criteriosa.
O preço da máquina não deve ser o único fator decisivo na sua escolha, mas sim um componente de um conjunto de considerações que incluem qualidade, capacidade, eficiência, suporte pós-venda e custos operacionais.
Primeiramente, é importante entender que o preço de uma injetora pode variar significativamente de acordo com diversos fatores, como tamanho, se será usada ou nova, sua capacidade, marca, tecnologia embarcada e país de origem.
Avalie diferentes opções disponíveis no mercado, levando em conta suas especificidades e benefícios oferecidos.
Financiamento e Formas de Pagamento
Quando se trata de adquirir uma injetora de plástico, o financiamento e as opções de pagamento desempenham um papel crucial na viabilização do investimento.
Entender as diferentes modalidades de financiamento e formas de pagamento disponíveis pode facilitar a aquisição da máquina e tornar o processo mais acessível para o seu negócio.
As opções de financiamento podem variar desde linhas de crédito específicas para a compra de maquinário industrial até leasing e financiamentos diretos com o fabricante.
É importante pesquisar e comparar as taxas de juros, prazos e condições oferecidas por diferentes instituições financeiras ou pelo próprio fabricante para encontrar a melhor opção que se encaixe no seu orçamento e fluxo de caixa.
Além das opções de financiamento, é essencial considerar as formas de pagamento disponíveis.
Muitas empresas oferecem diversas modalidades, como pagamento à vista com desconto, parcelamento sem juros no cartão de crédito, boleto bancário ou financiamento próprio.
Avalie cada opção cuidadosamente, levando em conta as suas necessidades financeiras e a disponibilidade de recursos no momento da compra.
É recomendado também negociar as condições de pagamento e buscar flexibilidade junto ao fornecedor.
Algumas empresas estão abertas a negociações e podem oferecer condições especiais ou descontos dependendo do volume da compra ou da relação comercial estabelecida.
Em resumo, ao considerar o financiamento e as formas de pagamento para a aquisição de uma injetora de plástico, é fundamental realizar uma análise detalhada das opções disponíveis, considerar as necessidades financeiras do seu negócio e negociar as melhores condições para garantir um investimento bem-sucedido e alinhado com as suas expectativas.
Custo com Moldes
O custo com moldes é um dos aspectos financeiros mais significativos a serem considerados na aquisição de uma injetora de plástico.
Os moldes são essenciais para a produção das peças e têm um impacto direto na qualidade, precisão e eficiência do processo de injeção.
É fundamental entender e planejar adequadamente esse investimento para garantir resultados satisfatórios e retorno sobre o investimento.
Os custos com moldes podem variar consideravelmente dependendo da complexidade, tamanho, material e acabamento das peças a serem produzidas.
Moldes mais complexos ou com detalhes refinados geralmente requerem um processo de fabricação mais elaborado e, consequentemente, um custo mais elevado.
Além disso, é importante considerar a vida útil do molde, que pode variar dependendo do material utilizado e do cuidado na manutenção.
Ao avaliar o custo com moldes, é recomendado solicitar orçamentos de diferentes fornecedores e comparar as opções disponíveis.
Lembre-se de considerar não apenas o preço, mas também a qualidade, durabilidade e o suporte oferecido pelo fabricante.
Optar por moldes de alta qualidade e durabilidade pode resultar em economia a longo prazo, reduzindo os custos de manutenção e substituição.
Além disso, é importante incluir os custos com moldes no planejamento financeiro da sua empresa e considerar a depreciação do investimento ao longo do tempo.
Planejar adequadamente o orçamento para a aquisição e manutenção de moldes garantirá uma produção contínua e eficiente, minimizando os riscos de paradas não programadas e maximizando a rentabilidade do seu negócio.
Em resumo, ao considerar o custo com moldes na aquisição de uma injetora de plástico, é essencial realizar uma análise detalhada, comparar as opções disponíveis e planejar adequadamente o investimento para garantir uma operação eficiente e rentável a longo prazo.
Custo de Energia Elétrica
O consumo de energia elétrica é um fator significativo que deve ser considerado ao se avaliar uma injetora de plástico, pois fará parte da composição do custo de cada peça e consequentemente no preço final para seu cliente.
A eficiência energética da máquina pode influenciar diretamente nos custos operacionais e na rentabilidade do seu negócio.
Portanto, é importante avaliar o consumo de energia da máquina e buscar opções mais eficientes para reduzir os custos e minimizar o impacto ambiental.
As injetoras de plástico estão disponíveis em diferentes modelos e tecnologias, e o consumo de energia pode variar consideravelmente entre eles.
Modelos mais antigos ou menos eficientes podem apresentar um consumo de energia mais elevado, enquanto máquinas mais modernas e tecnologicamente avançadas geralmente são projetadas para serem mais econômicas e sustentáveis.
Para avaliar o custo de energia elétrica, é recomendado verificar as especificações técnicas e o consumo energético declarado pelo fabricante.
Além disso, considere as condições de operação da máquina, como tempo de funcionamento, ciclos de produção e demanda de energia durante o processo de injeção.
Essas informações são essenciais para estimar os custos de energia e planejar adequadamente o orçamento operacional.
É válido também considerar a instalação de sistemas de monitoramento e controle de energia, que podem ajudar a otimizar o consumo e identificar oportunidades de economia.
Considere investir em treinamento da equipe para operar a máquina de forma eficiente e consciente pode contribuir para a redução do consumo de energia e o aumento da eficiência operacional.
Ao avaliar o custo de energia elétrica na aquisição de uma injetora de plástico, é essencial considerar a eficiência energética da máquina, verificar as especificações técnicas, estimar os custos operacionais e buscar oportunidades de economia para garantir uma operação sustentável e rentável a longo prazo.
Custo e Logística de Transporte da Máquina
O transporte da injetora de plástico é uma etapa crucial que envolve não apenas custos, mas também uma série de aspectos logísticos que devem ser cuidadosamente planejados para garantir uma operação segura e eficiente.
Seja na compra de uma máquina nova ou usada, a logística de transporte requer atenção especial para evitar contratempos e garantir que a máquina chegue ao destino em perfeitas condições.
Além dos custos associados ao transporte, é importante considerar outros fatores como seguro, distância e condições da estrada.
Contratar um seguro de transporte é uma medida prudente para proteger o investimento em caso de danos ou perdas durante o trajeto.
Verifique as opções de seguro disponíveis e as coberturas oferecidas para garantir uma proteção adequada para a sua máquina.
A distância entre o local de origem e o destino também é um aspecto a ser considerado na logística de transporte.
Quanto maior a distância, maiores podem ser os custos e os desafios logísticos envolvidos.
Em resumo, ao planejar o transporte da sua injetora de plástico, é essencial considerar não apenas os custos, mas também uma série de aspectos logísticos como seguro, distância, condições da estrada e necessidades de embalagem e proteção da máquina.
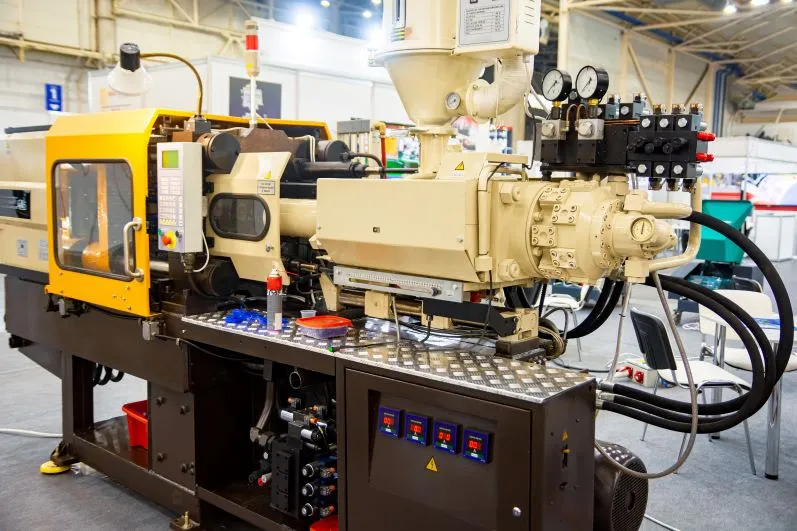
Temos um post sobre compra segura de máquina injetoras usadas.
Você pode conferir o texto clicando aqui.
Compra Segura da sua Injetora de Plástico
Ao investir em uma injetora de plástico, é fundamental realizar uma compra segura e bem planejada para garantir que você faça um investimento sólido e alinhado com as necessidades do seu negócio.
A segurança na compra vai além de apenas escolher a máquina certa; envolve uma série de cuidados e precauções que podem evitar problemas e assegurar uma transação tranquila e satisfatória.
Dicar para uma Compra Segura:
Pesquisa e Avaliação: Faça uma pesquisa detalhada sobre as marcas, modelos e fornecedores disponíveis no mercado. Avalie as especificações técnicas, reputação do fabricante e opiniões de outros clientes para tomar uma decisão informada.
Verificação de Documentação: Certifique-se de que todos os documentos relacionados à máquina, como nota fiscal, garantia e manuais, estão em ordem e atualizados.
Inspeção da Máquina: Se possível, visite pessoalmente o local onde a máquina está instalada ou solicite uma inspeção para verificar as condições reais e o funcionamento da máquina.
Negociação Transparente: Esteja aberto a negociar condições, preços e formas de pagamento.
Mantenha uma comunicação transparente e clara com o vendedor para evitar mal-entendidos e surpresas desagradáveis.
Contrato de Compra: Formalize a compra através de um contrato bem elaborado que detalhe todas as condições acordadas, incluindo preço, forma de pagamento, prazos e responsabilidades de ambas as partes.
Seguro de Transporte: Contrate um seguro de transporte adequado para proteger a máquina durante o transporte e garantir que qualquer dano ou perda seja devidamente coberto.
Acompanhamento Pós-Venda: Certifique-se de que o fornecedor oferece suporte pós-venda, assistência técnica e peças de reposição. Um bom relacionamento com o fornecedor pode ser crucial para resolver qualquer problema ou dúvida que possa surgir após a compra.
Conclusão:
A compra de uma injetora de plástico é um investimento significativo que requer cuidado, atenção e planejamento.
Seguir os passos acima e adotar uma abordagem cuidadosa e criteriosa na escolha da máquina e do fornecedor garantirá uma compra segura e bem-sucedida.
Lembre-se de que uma decisão informada e uma negociação transparente são fundamentais para evitar problemas e assegurar uma transação tranquila e satisfatória.
Ao priorizar a segurança e a qualidade na sua compra, você estará dando um passo importante para o sucesso e a eficiência do seu negócio no mercado de injeção de plástico.
Ao longo deste guia abrangente sobre injetoras de plástico, exploramos diversos aspectos essenciais que devem ser considerados ao adquirir uma máquina, desde a escolha do tipo e capacidade até os custos e logística envolvidos na compra.
